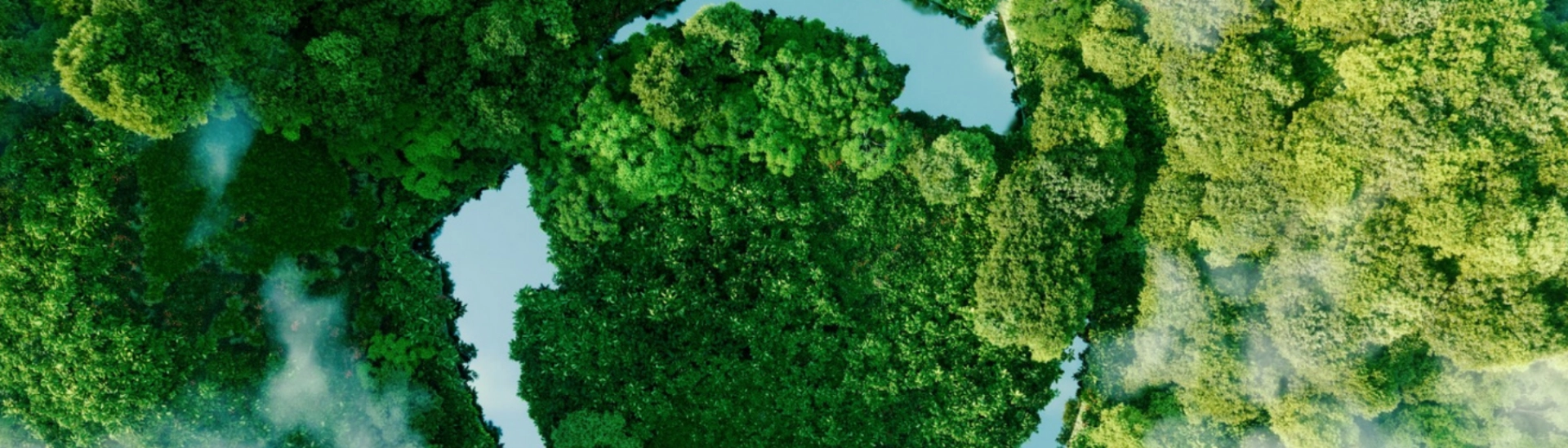
Now the concept of circularity has gained significant traction in the manufacturing industry. Circularity is a paradigm shift that encourages the development of closed-loop systems, aiming to minimize resource consumption, waste generation, and promote the reuse and recycling of products. This article explores the importance of circularity in the manufacturing industry, its key principles, and the benefits it offers in fostering a sustainable future.
What is Circularity in Manufacturing Industry?
Circularity is a holistic approach that aims to close the loop of resource usage in the manufacturing industry. Traditionally, the industry has followed a linear model known as the "take-make-dispose" model. In this linear approach, resources are extracted, processed into products, and ultimately discarded as waste. Circularity, on the other hand, seeks to replace this linear model with a closed-loop system where resources and materials are continuously recycled, reused, or repurposed, minimizing waste and reducing the strain on the environment.
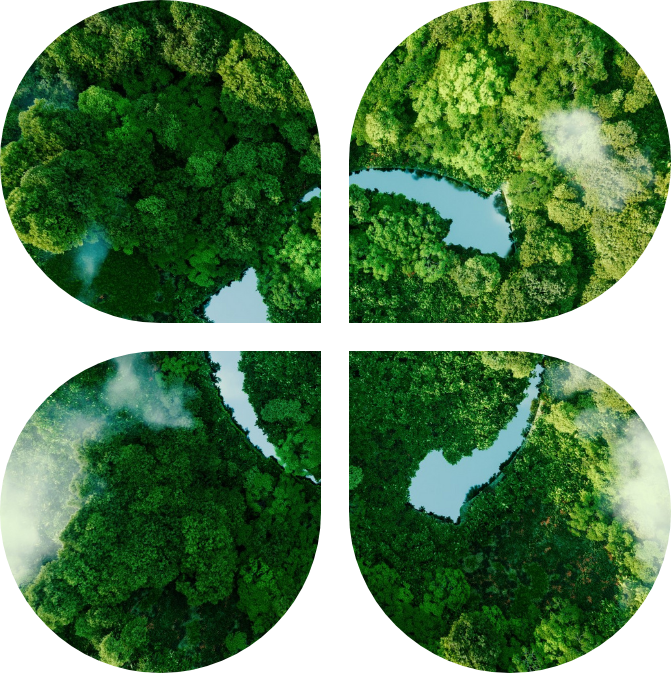
Key Principles of Circularity:


Designing for Durability:
Circular manufacturing starts with product design. Manufacturers are encouraged to design products that are built to last, using durable materials and components. This approach not only extends the product's lifespan but also reduces the need for frequent replacements and minimizes waste generation.


Reusing and Refurbishing:
Instead of discarding products after use, circularity promotes the reuse and refurbishment of items. Manufacturers can establish mechanisms to collect, repair, and upgrade products, extending their lifespan and reducing the demand for new resource extraction.
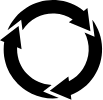
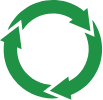
Recycling and Material Recovery:
Circular manufacturing emphasizes the effective recycling and recovery of materials from end-of-life products. By implementing efficient recycling processes, manufacturers can extract valuable materials and reintegrate them into new production cycles, reducing the reliance on virgin resources.


Waste Reduction:
Circularity aims to minimize waste generation at every stage of the manufacturing process. This involves implementing measures such as lean production techniques, efficient material management, and waste-to-energy conversion to ensure that resources are utilized optimally, and waste is minimized.
Important aspects of circularity in the manufacturing industry:
- Life Cycle Thinking:Circular manufacturing involves adopting a life cycle approach to product design and development. It considers the entire life cycle of a product, from raw material extraction to disposal, and aims to minimize environmental impacts and optimize resource efficiency at each stage.
- Sustainable Material Selection:Circular manufacturing prioritizes the use of sustainable and recyclable materials. Manufacturers seek alternatives to non-renewable resources and focus on selecting materials that can be easily recycled, reused, or repurposed at the end of a product's life.
- Product Design for Disassembly: Designing products for disassembly is a fundamental principle of circularity. Manufacturers should ensure that products are designed in a way that allows for easy separation of components and materials during the end-of-life phase. This facilitates efficient recycling and reduces the energy and effort required for material recovery.
- Reverse Logistics and Take-Back Programs: Circular manufacturing encourages the implementation of reverse logistics and take-back programs. Manufacturers establish mechanisms for collecting and retrieving products at the end of their useful life, enabling proper recycling, refurbishment, or remanufacturing.
- Extended Producer Responsibility (EPR): EPR is a policy approach that holds manufacturers accountable for the entire life cycle of their products, including their proper disposal. It incentivizes manufacturers to design products with end-of-life considerations in mind and promotes the establishment of recycling and recovery systems.
- Collaborative Partnerships: Achieving circularity often requires collaboration between various stakeholders in the manufacturing industry. This includes partnerships with suppliers, customers, waste management companies, and recycling facilities. Collaborative efforts facilitate the efficient flow of materials, information, and resources throughout the value chain.
- Digitalization and Technology Adoption: Digitalization plays a crucial role in enabling circular manufacturing. Technologies such as the Internet of Things (IoT), artificial intelligence (AI), and data analytics can optimize material flows, enable real-time monitoring of products, and facilitate effective waste management and recycling processes.
- Education and Awareness: Promoting education and awareness about circularity is essential for its successful implementation in the manufacturing industry. Manufacturers should invest in training programs for employees and raise awareness among consumers, encouraging responsible consumption and the importance of recycling and reuse.
- Circular Economy Business Models: Circular manufacturing encourages the adoption of innovative business models that support circularity. Examples include leasing and sharing models, where customers have access to products without the need for ownership, and servitization, where manufacturers shift from selling products to providing services or solutions.
- Continuous Improvement and Measurement: Circular manufacturing is an ongoing journey of continuous improvement. Manufacturers should establish key performance indicators (KPIs) to measure their progress towards circularity goals. Regular monitoring, evaluation, and feedback loops help identify areas for improvement and drive further advancements in circular practices.
- Resource Efficiency: By reducing waste and increasing material efficiency, circular production aims to maximize resource utilization. This involves reducing material waste throughout production processes, utilizing recycled or renewable materials, and putting effective manufacturing strategies like just-in-time production and lean manufacturing into practice.
- Closed-Loop Supply Chains: Creating closed-loop supply chains, where products and materials are kept as much as possible inside the system, is a key component of circular manufacturing. This may involve tactics like product return policies, the remanufacturing or refurbishing of products, and the use of recycled materials in the production of new products.
Benefits of Circularity in the Manufacturing Industry:
- Environmental Preservation: Embracing circularity helps to alleviate the environmental impact of the manufacturing industry. By reducing resource consumption and waste generation, circular practices contribute to the conservation of natural resources, reduction of greenhouse gas emissions, and preservation of ecosystems.
- Cost Savings: Circular manufacturing can result in significant cost savings for companies. By extending the lifespan of products through refurbishment and reuse, manufacturers can reduce the need for raw material procurement and decrease production costs. Moreover, effective waste management and recycling can generate additional revenue streams from recovered materials.
- Enhanced Reputation: Adopting circularity principles not only aligns businesses with sustainable development goals but also enhances their reputation among consumers, investors, and stakeholders. By demonstrating a commitment to environmental stewardship, manufacturers can build trust and loyalty among environmentally conscious customers.
- Resource Resilience: Circularity reduces dependence on finite resources by promoting the use of recycled and repurposed materials. This helps to create a more resilient supply chain that is less susceptible to fluctuations in resource availability and prices
Circularity presents a transformative opportunity for the manufacturing industry to transition towards a more sustainable and regenerative model. By embracing the principles of circularity, manufacturers can reduce resource consumption, minimize waste generation, and create closed-loop systems that enable the reuse, recycling, and repurposing of products. Embracing circularity not only benefits the environment but also offers economic advantages, enhances reputation, and promotes resource resilience. As we strive for a sustainable future, circularity emerges as a key driver for positive change in the manufacturing industry.